Blog: Business
Business Benefits of a LIMS
30th January 2020
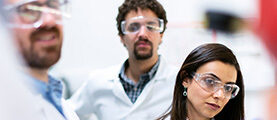
Ensuring regulatory compliance, reducing errors, streamlining workflows and enabling growth through the introduction, consolidation and integration of IT systems will ultimately pay dividends for the business and help achieve a competitive advantage. However, for many reasons including lack of resources, no formal business plan or the difficulty of articulating the potential business benefits, laboratories often struggle to drive the introduction and modernization of IT solutions in their laboratories.
Autoscribe Informatics works with companies worldwide to improve business efficiency. Our Xybion LIMS Laboratory Information Management System (LIMS) drives consolidation, improves data integrity and increases laboratory efficiency. Laboratory process automation and workflow management can reduce transcription errors, improve turn-around times, and increase resource utilization; and these are just a few of the business benefits associated with adopting a LIMS.
Paper is Bad for your Laboratory
Many organizations continue to use paper and spreadsheets to record formal laboratory test results even though this has been shown to be error-prone. Studies typically cite a transcription error rate of between 3% and 5%, some even more. One academic study of transcription errors in laboratory data in an intensive care unit at Glasgow Royal Infirmary found an 8.8% error rate [Ref 1]. Another study by the Royal Society of Chemistry in the UK [Ref 2] concluded that “to err is human” with the most common cause of poor results being human error. Reducing such errors would significantly improve the overall accuracy of reported results.
Transcription errors have been known in laboratories for years. Tried and tested methods of overcoming these limitations include contemporaneous result approval and double-blind data entry, however, these can be resource-intensive. For example, by using a LIMS and automatically capturing test results from laboratory instruments transcription errors can be eliminated. Xybion LIMS can accept instrument interfaces via three methodologies:
- The CSV/TXT file interface currently covers 80% of instrument connections in the laboratory. The instrument output, in the form of a text file, is captured and read by the LIMS and the test result(s) are automatically recorded. Interfaces may be two way, allowing instrument parameters and sample lists to be passed to the instrument from the LIMS.
- Serial interfaces such as RS232/422, are used by many simpler instruments such as balances. These can be connected directly to a PC or network interface device from which the LIMS captures results as they are generated.
- Direct integration with other data systems such as Chromatography Data Systems (CDS) can be implemented, often using Application Programming Interfaces (APIs). Again, this can be bi-directional.
Apart from the elimination of transcription errors instrument integration also speeds up turn-around-time (TAT) in the laboratory. Keeping expensive instruments running at full capacity can dramatically improve the efficiency and profitability of your laboratory. While transcription errors in paper-based systems are bad enough, relying on spreadsheets to run your business can be even more problematic. While the issue of transcription errors still exists in manually populated spreadsheets, the spreadsheets themselves can be a source of error. One often-cited study from the University of Hawaii [Ref 3] found that 88% of spreadsheets in use contained errors. Furthermore, the study found that errors in formulae are extremely difficult to spot (especially complex scientific type formulae that can pull data from multiple spreadsheets) yet, once developed, end users quickly became overconfident in the accuracy of the bottom-line values. Trying to understand and correct a complex spreadsheet, especially if created by someone else, is difficult and the temptation can be to start over again. It can also be difficult to control changes to spreadsheet functionality and calculations once in use; all of which can call into question the integrity of data managed through spreadsheets. The same functionality can be implemented in LIMS, however in this case changes to data can be recorded through the use of an audit trail, and the ability to alter calculations, for example, can be limited to authorized personnel only. Using a LIMS also ensures that all your laboratory data is kept in a single database rather than spread across multiple filing cabinets (possibly in multiple rooms) if using paper records, or multiple computer files on a central server (or even individual PCs) when using spreadsheets. Centralization of the data in a single database makes it easier to access and use that data, for example in the generation of Statistical Process Control charts or for Analytical Quality Control purposes, and it can quickly alert the organization to potential problems.
The Cost of Getting It Wrong
Product recalls cost industries millions of dollars every year. Yet with proper controls in place and a strong lead from management, many of them could be avoided. In 2008 Ranbaxy Laboratories were one of the largest providers of generic drugs in India and many other countries, including the United States. Ranbaxy was bought by Daiichi Sankyo for $2.4 billion but the deal began unravelling when manufacturing violations came to light that prompted the US Food and Drug Administration (FDA) to ban more than two dozen Ranbaxy drugs from entering the USA [Ref 4]. The scandal cost Ranbaxy $500M while the FDA extended the list of banned Ranbaxy drugs to two more plants following further inspections impacting the business even more. Systemic QC failures, at all levels, appeared to be the main downfall of Ranbaxy. By implementing and supporting QC procedures within a LIMS it becomes much more difficult to circumvent the Quality System, either by mistake or on purpose.
Another well-documented example is the China Baby Milk Scandal where production problems cost a large milk manufacturer $700m [Ref 5]. The troubles related to baby milk cartons for the Chinese market being mislabeled. Cautious Chinese parents, already hit by a milk powder scare in 2008 that killed six babies and hospitalized thousands more, shied away from the product seriously impacting sales revenue and market share. It’s what every business hopes never happens – costly recalls that hurt immediate profits and damage the brand for years to come. The questions every production business has to ask are – what is the cost of getting it wrong? How much would a full product recall cost? What is the risk to human life and health? How large could the regulatory fines be? And what could be the cost of loss of brand reputation and future sales?
All organizations have to weigh up costs vs returns. It is incumbent upon safety, regulatory and QC functions within any organization to bring the huge potential costs of a production or QC failure to the attention of senior management and ensure that quality remains at the heart of the organization. Following strict standards such as ISO17025, FDA 21 CFR Part 11, GxP (Good Laboratory Practice, Good Manufacturing Practice etc.) that are appropriate to your industry help. Capturing the working methodology behind standards in standard operating procedures (SOPs) and using a LIMS to implement SOPs as workflows as well as to capture the required data provides the level of control businesses require and regulators increasingly demand.
Forging a Better Path
One way of further exploring the costs and benefits of a LIMS and driving best practices within your organization is to download the white paper “Justifying the Purchase of a LIMS”. It is packed with advice on building a business case for the purchase of a LIMS. When considering your current costs it is often the time spent connecting the data manually, finding the right data within all those paper records and building management reports to help control the business, which uses a significant amount of operational and management time.
Every business (and laboratory) is different, and yet they are all the same. For those exploring the business benefits of a LIMS whether in a laboratory, in a Quality/Regulator role or at the C-level it cannot be just a question of the cost. There will be a cost associated with implementing an integrated laboratory management system that eliminates paper records, ensures data integrity, drives data analytics and ensures ‘quality’ in all its forms; however equally important is the cost of NOT doing so - the cost of not streamlining processes and building in quality from the ground up. The examples cited above are not isolated cases and, as has been illustrated, the costs of getting it wrong can become enormous. Ultimately it could be fatal to your business.