Blog: Industry
The Importance of Batch Control in Manufacturing LIMS
18th June 2024
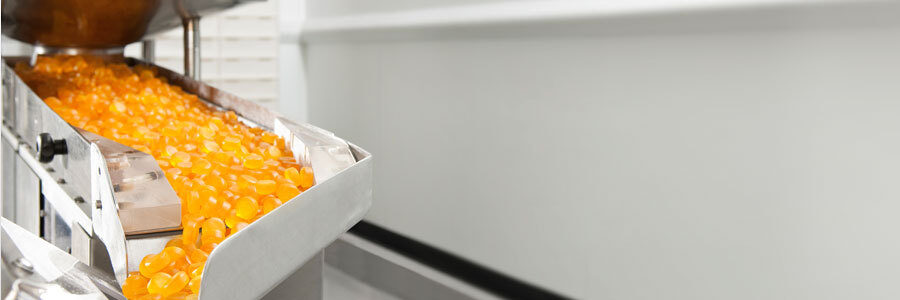
In batch manufacturing products move through the production process in discrete steps. Quality control checks may occur at each stage before the product is released to market or for further processing. The release of the final product only occurs on successful completion of all the QA checks in the manufacturing process. A good current example of batch control that we hear of every day is the release of Covid-19 vaccine. Raw ingredients, which are tested on receipt to ensure the correct quality, are added to a bioreactor{1} and the vaccine grown over several days. Once completed this intermediate product is transferred from the bioreactor to an isolated storage vessel. Testing is then performed to ensure potency and purity of the solution. The product is then transferred to a fill and finish plant where it is bottled, labelled, and again held while further samples are taken for testing. If testing confirms the quality of the product the vaccine is released for distribution to vaccine centers and use. The vaccine is held in storage awaiting test results at both intermediate and fill and finish product stages which can take many days, causing an inevitable stock buildup and lag in the system. Whilst quality control testing is usually invisible to the public, in a world which awaits vaccine via 24/7 news updates this time lag becomes highly visible.
Figure 1: The Regulated Manufacturing Workflow - Out-of-box configuration
The manufacturing process is closely monitored throughout. Traceability is key and it must be possible to link batches of materials used to the testing carried out during the process. Should any issues be found, the source can be identified and if the problem lies in a raw material or intermediate material batch the concept of traceability means any other products those batches have been used in can be identified.
In a laboratory where discrete samples are presented for test the linkage between various sample types are not required. Contract laboratories where samples are sent for test, water laboratories where water samples are collected from multiple locations, and Covid testing laboratories where individual samples are tested, are typical examples of discrete testing.
In these flows, samples are registered, received, tested, validated, and approved largely individually. Samples may be related and compared by sample type, supplier, batch and so forth but each sample is discrete in a non-batch manufacturing laboratory.
By contrast, in a Manufacturing flow samples from across the entire production line, and of very different types, are related. This relationship must be known by the laboratory for traceability purposes. It is this linkage that defines a Manufacturing LIMS from a simple monitoring LIMS. Autoscribe provides dedicated starter systems for both types of laboratory, ensuring that all the key requirements of a LIMS for those environments are already built into the system. This saves considerable time and cost in deploying the LIMS and going ‘live’ in a laboratory.
Key Elements of a Manufacturing LIMS
In a Manufacturing LIMS, materials and their associated samples are classified as Raw Materials (RM), Intermediate Products (IP), or Final Products (FP). IP and FP types can have a defined recipe which specifies the component materials (which may be IPs as well as RMs) and volumes of each that make up the product. As an example, in the brewing industry, Wort (an IP) is made from the raw ingredients Malted Barley and Water. The amount of each RM to use can be defined as a Recipe within the LIMS. Multiple wort recipes may exist for different types of beer.
The different Raw Material batches used must be recorded in the LIMS for traceability purposes. If a problem is found that can be traced to a specific batch of RM the information associated with the batch record means that it can be tracked to supplier, and action taken as required.
Required tests can be automatically assigned to batches based on the materials to be tested, and product specific specifications applied. These identify any test results that are outside the defined product specifications.
The LIMS holds the information required for testing of specific products, including recipes, within pre-defined Batch Templates. Using these the laboratory can quickly register each new batch that is started. This includes the sample and associated tests required at the different stages on the batch process. On completion of the manufacturing process and associated testing batch approval releases the product for use.
Key parts of a manufacturing LIMS include:
- Material and Supplier Management – specifies RM and its sources
- Recipe Management – defines components of IP & FP
- Specification & Test Group Management – defines required testing and product or material test specifications
- Batch Template Management – Models the manufacturing process and associated information within the LIMS
Figure 2: Maintenance Dashboard of the Regulated Manufacturing Workflow - Key Batch Manufacturing Components
Why is this different to Non-Batch Manufacturing Laboratories?
Products are typically manufactured to a set of defined manufacturing specifications. However other product specifications may exist for specific customers or markets. It can therefore be important to check what other specifications a product meets. Batch Grading functionality allows the product to be assessed against multiple specifications. In this way a batch of product can be matched to the most suitable market or customer, maximizing its value.
A LIMS, however, is not just limited to managing product testing. An integrated LIMS solution should have other modules that assist in the running and management of the laboratory, these include User Competency, Instrument Calibration & Maintenance, CAPA, and Laboratory (Chemicals) Inventory Management.
Flexibility Remains Key
Despite many similarities no two manufacturing laboratories are ever identical in the way they work, or the data they must capture. Xybion LIMS is built around a genuinely configurable approach. Using graphical configuration tools, screens and workflows, and the functionality behind them, can be modified to meet specific needs. This is done without software coding and is isolated from the underlying Xybion LIMS product software.
This has a huge impact on the flexibility of the system, making it easy and cost effective to define specific workflows for particular users, or types of users. These can be as simple or as complex as required and, once they have been implemented, this configured functionality is not impacted by future developments of the underlying software that Autoscribe release. So confident are we of this that not only do we undertake to support any configuration work that we may do for our customers we also support configuration work they may choose to do themselves.
References:
1: Covid-19 vaccine production processes vary. References to two examples of vacine production processes are described here: