Blog: Business
Using LIMS to Improve Business Efficiency and Profitability
16th September 2020
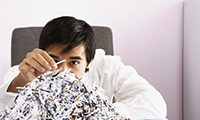
The Model T Ford is still discussed in business schools today because of how Henry Ford relentlessly drove quality and innovation. When first introduced in 1908 the Model T cost $825; by 1916 it cost $360. While reducing the cost by more than half, Ford increased the safety, reliability, and speed of the product. His laser-like focus on quality was legendary and his quote “Quality means doing it right when no one is looking”, is still a mainstay of quality theory and practice.
Whether manufacturing cars, supplying clean water, or manufacturing pharmaceuticals, all repeated processes must include quality control to ensure products meet their defined requirements. Quality management is very often about measuring and minimizing variance within and across batches to ensure adherence to acceptable limits. This in turn is all about keeping meticulous records, as well as managing and accessing that data.
Paper is Bad for Your Laboratory (And Your Health)
Many QC laboratories still use paper and pen or spreadsheets to record test results. Both can be very bad for your laboratory and ultimately your profit line. A study in 2004 at the Glasgow Royal Infirmary[1] quantified the transcription error rate for blood results by comparing the handwritten and printed laboratory results in 100 patients in the intensive care unit of the hospital. It concluded that errors in transcription rates averaged 8.8% and argued the case for computerization of the patient records to eliminate these errors.
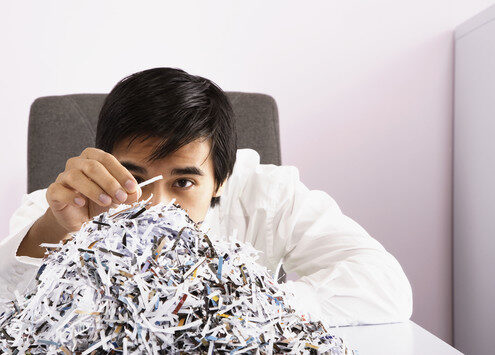
A study in the University of Hawaii set out to analyze the errors embedded in spreadsheets[2]. After auditing 88 different spreadsheets it found that 94% of them contained errors, either in the data entered or the calculations within the spreadsheet. This is a powerful argument to remove manual data entry and enforce proper management and validation of calculations for derived results; functions ideally suited to a Laboratory Information Management System (LIMS).
Eliminating human error, by copying results incorrectly, remains at the very heart of why a LIMS is so important. As the Royal Society of Chemistry[3] put it ‘to err is human’. The report concluded that focusing on elimination of human error can have one of the biggest impacts on analytical quality.
Improving TAT and Data Integrity with Instrument Integration
Autoscribe’s Matrix Instrument Data Acquisition System (MIDAS) enables the collection of results from a wide variety of instruments, automatically extracting the data it needs and passing it into the LIMS. Completely eliminating human interaction eradicates typographical errors and mistakes in calculation, providing repeatable quality every time and ensuring the integrity of the data recorded. In addition, MIDAS speeds up the capture of results from instruments, vastly improving the efficiency of the laboratory and enabling analysts to concentrate on higher value tasks.
Managing Your Data
Paper records in a notebook can work well in a small laboratory but there comes a point where the data ‘mountain’ becomes unmanageable. For example, data held in separate notebooks can complicate the process of creating the final certificate of analysis for a product or sample. Very often historical data, in the form of paper records, will build over time to fill several filing cabinets or even rooms, making it almost impossible to find and compare data sets quickly.
Processes such as searching and comparing data, re-creating and reissuing certificates of analysis, producing laboratory management reports, managing instrument calibration records and staff competency, controlling inventory, and ensuring compliance with standard operating procedures, are all easier with data in a single accessible database. Effective and efficient data management, more than any other single reason, is why laboratory managers turn to a LIMS. The time savings associated with this alone often justifies the purchase of a LIMS.
The Cost of Getting it Wrong
There are many examples of costly product recalls when things go badly wrong. Ranbaxy Laboratories, a generic drug maker in the pharmaceutical industry, and one of the largest providers of generic drugs in India at the time, is one that is often cited[4]. Ranbaxy was sold to Daiichi Sankyo for $2.4 billion, but the deal was soon caught up in quality control issues.
Within months, the US FDA had banned more than two dozen drugs due to quality control problems at Ranbaxy involving improper testing of medicines. Ranbaxy pleaded guilty and paid $500 million in fines to the US, but then the FDA banned drugs from two more Ranbaxy plants following further inspections, prompting Daiichi to sue the former owners for $400 million in damages.

The cost of not following the rules, and not managing quality, can be very large indeed in regulated and safety critical markets. A LIMS provides a defendable quality control framework and, through standard operating procedures, ensures repeatable quality that you can trust.
It’s not just the immediate loss of business when a manufacturing plant stops that has an impact; it is also the future loss of earnings when consumer confidence is lost. Indeed, losing consumer trust can be even more costly. It is claimed that the 2008 contaminated milk scandal in China cost Fonterra up to $700 million[5,6]. The scandal involved infant formula milk being adulterated with melamine. The chemical was used to increase the nitrogen content of milk, giving it the appearance of higher protein content to pass product quality standards. 54,000 babies were hospitalized, and 6 babies died. Chinese dairy farmers had unwittingly added ‘protein powder’ to the milk to ensure it was not rejected. This adulteration was not detected during testing by Sanlu (43% owned by Fonterra at the time). The scandal caused widespread product recalls, a loss of consumer confidence within China, and led to other countries banning formula milk imports from China. It has taken many years for the Chinese dairy industry to recover, with much improved quality control testing now in place. The loss of brand reputation can indeed cost you dear.
LIMS Increases Efficiency and Manages Risk
Whether your laboratory is regulated or not, and whatever type of testing it performs a LIMS will help you lower risk, reduce turnaround time, improve efficiency, and lower costs.
Key efficiency gains come from:
- Linking islands of data
- Abolishing typographical errors
- Reducing lab turnaround time and speeding product release
- Decreasing the risk of product recalls
- Increased resource efficiency
- Improved data accessibility and recall
- Enhanced management statistics and reporting
- Ensuring adherence to agreed standards (ISO17025, GxP, 21 CFR part 11)
- Managing risk and liability
Whether it is the reputational risk of delivering poor quality product, the need to reduce errors and re-testing of samples, or the pressure to work more efficiently, taking time to understand the business benefits a LIMS enables you to focus on improving your business, and your bottom line.
Justifying the Purchase of a LIMS - White Paper
Creating a return-on-investment (ROI) analysis and business case for implementing a LIMS can be daunting and yet it is often the first step in creating your business case for a LIMS. Find out more and download the white paper from here.
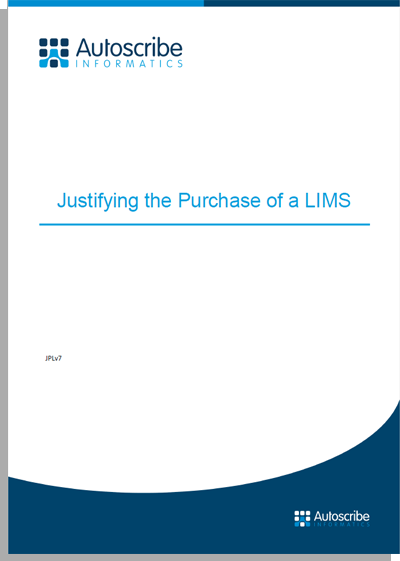
References
[1] Variation in the transcription of laboratory data in an intensive care unit. Black et al. Glasgow Royal Infirmary. Journal of Anaesthesia, 2004. [1]
The error rate of passing lab results to an intensive care unit. In summary they discovered an 8.8% error rate, with a greater chance of errors in the afternoon versus the morning. Their summary was that an electronic system would help reduce the errors.
[2] What We Know About Spreadsheet Errors. Panko. University of Hawaii [2]
A summary analysis of audits involving real world spreadsheets found 94% of the 88 spreadsheets audited contained errors. 20-40% of all spreadsheets contain errors.
[3] What causes most errors in chemical analysis? Royal Society of Chemistry, UK. [3]
This study concludes that “to err is human”. The results suggest that significant improvements could be made with more attention to the reduction of basic human errors.
[4] Daiichi wins $400M in damages over Ranbaxy drug safety scandal, May 2016 [4]
[5] Fonterra’s China partner warned over product mislabeling [5]
[6] 2008 Chinese milk scandal [6]